This method of 3D printing is referred to as streolithography (abbreviation SLA), or 3D printing by light curing, light polymerization or resin 3D printing. It is further divided into 3 different technologies:
-
Laser-based stereolithography
-
Digital Light Procesing (DLP)
-
Liquid crystal display (LCD).
How the basic principle of photopolymerization 3D printing works
It is a method of creating objects using gradual curing of polymers under the influence of radiation of different wavelengths, most often UV radiation. By focusing the radiation on a specific place, a layer of partially cured polymer or resin is created. Additional layers are applied to it. The object is thus created from layers.
This is one of the most accurate 3D printing methods: the theoretical accuracy corresponds to the size of the polymer molecule. This is much smaller than the thickness of a human hair - it is measured in μm (micrometers) - thousandths of a millimeter.
History
It is the oldest method of 3D printing. Its origins go back to the 70s of the 20th century with the research of the Japanese scientist Dr. Hideo Kodama. In 1984, Chuck Hull applied for a patent for this technology. Shortly after, a French team of scientists applied for a similar patent, but they did not complete their patent negotiations because the technology did not seem promising to them.
In 1986, a patent for stereolithography was granted to Chuck Hull, who founded 3D Systems Inc. A period video from 1989 shows that already in those times 3D printing attracted the media. His 3D printing method was based on curing the resin with a UV laser beam.
For the next 20 years, stereolithography went through its initial development. The resulting prints were not perfect, as deviations occurred during the hardening of the material. And most importantly - these 3D printers were incredibly expensive and required demanding maintenance. Yet their potential was irreversible.
Industrial 3D printers based on stereolithography were also developed by EOS, Solidscape (now part of Stratasys) or Objet Geometries Ltd (also acquired by Stratasys).
In September 2011, three MIT students founded FormLabs. In their successful campaign on the crowdfunding website Kickstarter, they raised 3 million USD and started production of the first desktop SLA 3D printers. In the same year, the Australian company Asiga came up with a new technology based on the curing of resin using an ultra-detailed projector. This technology enabled even faster and more detailed 3D printing - and most importantly, it was more affordable.
The third technology of this 3D printing, LCD, is still relatively young. It benefits from the low price of LCD screens in the size of a mobile phone or tablet and opens the door to an even wider spread of this method.
Trends
In the last few years, the SLA method of 3D printing has been experiencing a huge boom that is not going to end anytime soon. The number of manufacturers of 3D printers, especially those based on DLP or LCD technology, is constantly increasing. Related to this is the unprecedented interest of large chemical corporations in producing and improving photosensitive resins intended for this type of 3D printers.
Today, you can choose from a wide range of materials with different physical properties. They differ in stiffness, flexibility, fragility, elasticity, temperature or chemical resistance, shrinkage, and also in how they can maintain these properties over time. It is therefore not only about materials for prototyping, but also about materials suitable for the production of final products and parts.
The range of materials is constantly expanding. For use in production, wax or fusible materials are very interesting, allowing the simple creation of molds for mass production. 3D printing from ceramic materials is rapidly developing for everyday use in the field of dentistry as well. Silicone resins, developed by the German company Wacker Chemie, are also attractive for professional use.
The prices of industrial DLP printers are in the hundreds of thousands of CZK, while you can buy LCD printers for just a few tens of thousands of CZK.
Although the price of these 3D printers is constantly decreasing, they are not ideal for hobby use. 3D prints from them have to go through a post production process. First cleaning with isopropyl alcohol in an ultrasonic cleaner and then curing in a UV lamp. But they will certainly find their place as part of the production processes of ordinary engineering companies, in dental laboratories, in the production of custom-made hearing aids, in medicine, as a supplement in injection molding plants, in smaller studios of product designers and architects or developers.
When using these 3D printers, it is necessary to follow the principles of occupational safety. Resins are handled with rubber gloves, including prints during post processing. Resin and other necessary chemicals must be properly stored, labeled and kept out of the reach of children.
Advantages
-
speed - functional parts produced in a few hours
-
extreme level of detail - measured in micrometers (thousandths of a millimeter)
-
the almost smooth surface does not need additional surface treatment - thanks to the height of the layer, which is imperceptible to the human eye
-
large print area compared to other 3D printing methods
-
a great choice for serial production of functional parts
-
speeding up the casting process when the master model comes from a 3D printer
-
white and transparent resins can be pigmented according to customer preferences.
Disadvantages
-
still relatively high prices of photosensitive resins ranging in thousands of CZK
-
3D print must go through post processing
-
the necessity to observe the principles of occupational safety
-
the need to use supports for more complex geometries - there is a risk of the entire model collapsing and these places will not have a smooth surface
-
a wide range of materials requires expertise.
Are you intrigued by these new 3D printing technologies? We are the biggest expert in the Czech Republic in DLP and LCD 3D printing. We have tested and are constantly testing dozens of materials from manufacturers around the world. We will advise you on choosing the most suitable 3D printer and resin. Or choose the easiest way - send us your 3D model and we will print it for you. Contact us..
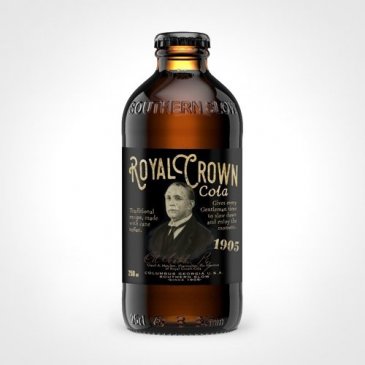
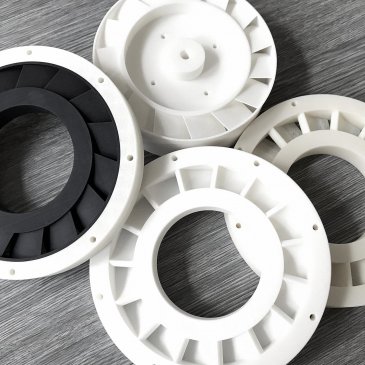
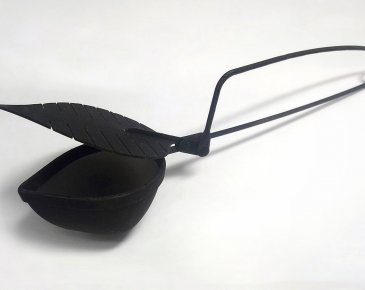
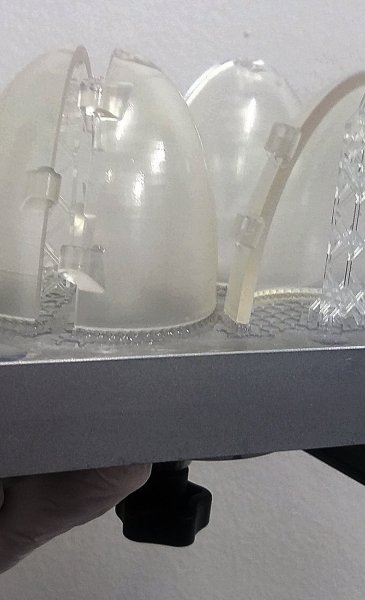
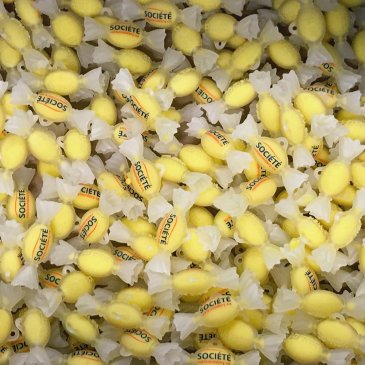
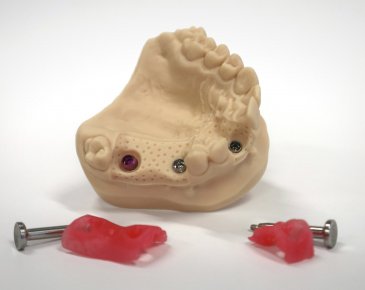
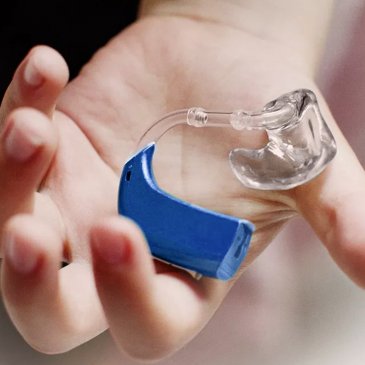
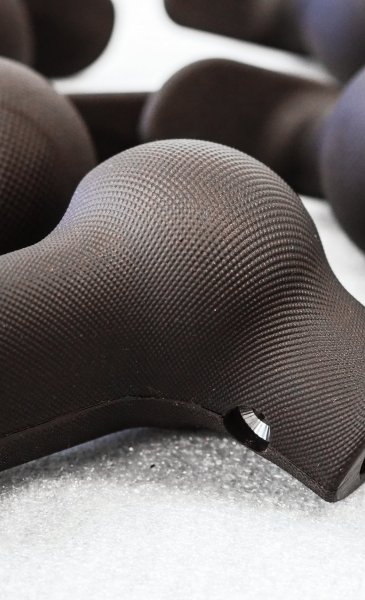
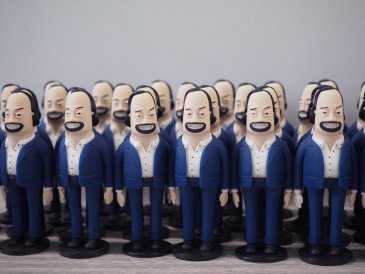
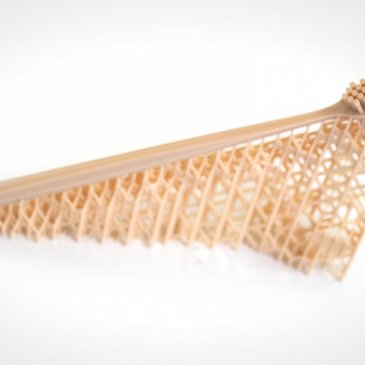
